Defects in optics and defect driven laser damage
Optical elements used for lasers are imperfect. Even a super polished glass surfaces hide thousands of defects upon and beyond the top layer.
Defects are various infringements such as cracks, scratches, digs, or impurities that causes optical element to break faster or at much lower fluencies than it was initially intended to be.
Damage threshold of classical dielectric optics is typically limited by localized defects – damage precursors. Most of them are created during optics manufacturing processes such as grinding, polishing or deposition of optical coatings. Defected area might trail several microns beneath the top layer.
A defect-free bulk material is covered by several machining effected zones [see fig. for details].
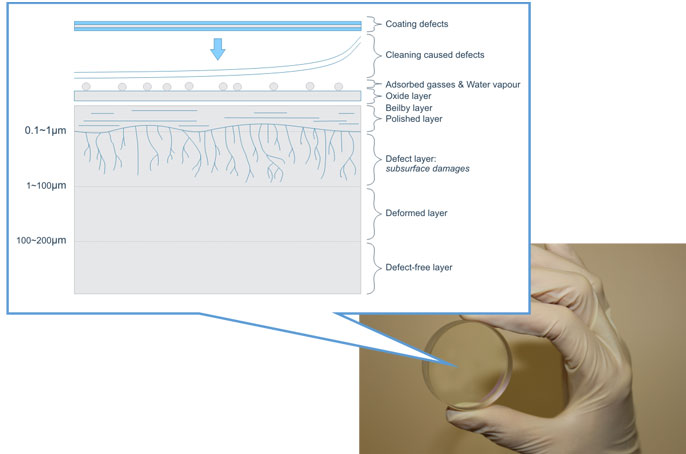
Fig. 1 Schematic illustration of defect’s layers on the optical material.
Firstly, grinding initiates deformation of the sub-surface and creates plenty of micro cracks due to friction between material and abrasives. Later, polishing conceals these defects with an amorphous structure, called the “Beilby” layer, that might contain various impurities, residuals of polishing slurry or abrasive material. Finally there is an oxide layer and adsorbed gases or water vapor layer. These are formed due surface interaction with outer environment. Contamination layers can be added on top, due to poor cleaning, packing or handling. Finally, deposition of optical coatings, might introduce nodular defects.